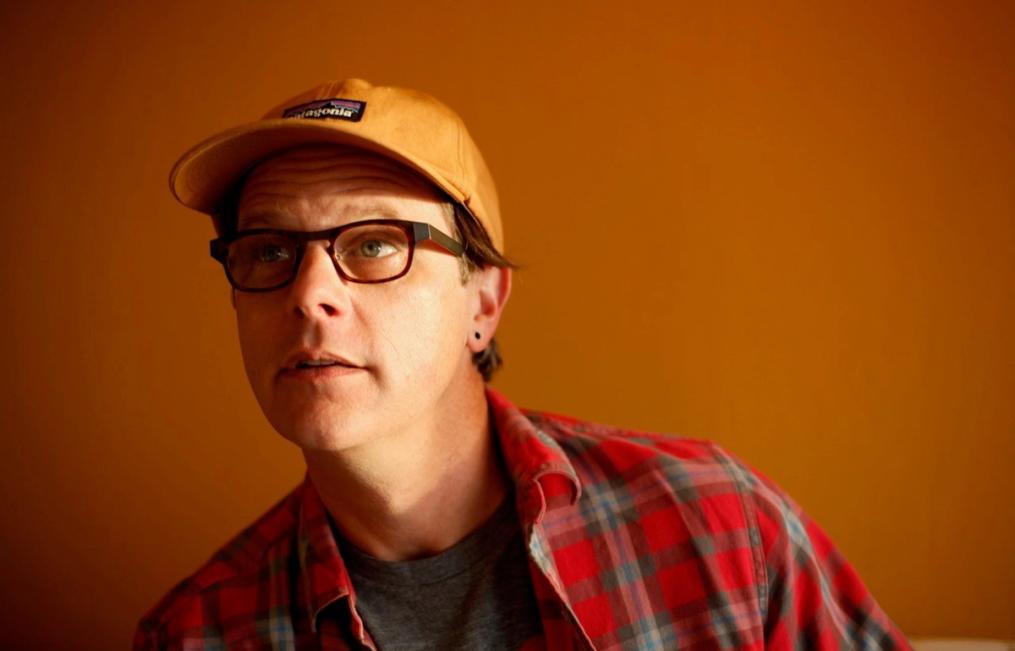
Craft: Chris French Metal
In the next installment of our CRAFT series, we spoke with Chris French, founder of Chris French Metal. Formally established in 2001 CFM has grown into a talented and highly skilled team of artists, designers, and fabricators, a meticulous studio providing high quality details and services to many of our best projects.
How did you first start honing your craft? Tell me about your background in fine arts.
Art was an accident; our whole business was somewhat of an accident. I grew up building; starting with LEGOs, which evolved into skateboard ramps, then speaker boxes for my low rider, and later furniture for my bedroom. I was simply doing what I knew how to do and what I was good at. I was not a good student, school was very hard for me, but in drafting class and wood shop I was the quintessential ‘A’ student. I wasn’t raised in an academic environment and had no basis to articulate what specifically interested me – this meant my discovery of “craft” happened later in life.
It wasn’t until I met an incredible group of friends at Arizona State University that I knew I could do something with the “craft” I had been inadvertently developing throughout my life. I graduated from ASU with a BFA in Sculpture and immediately moved to San Francisco in March of 1997. I was doing the typical artist thing back then – get a gallery in as many states as you could, create a new body of work every two years, and ship it around for exhibition. I had success with this model, but struggled with the artist’s statements and academically articulating the conceptual aspects of my work. I felt like I was right back in school.
Simultaneously, I was making functional objects for people and those functional objects became handrails, guardrails, and eventually a spiral staircase. This pragmatic approach to metal fabrication scratched a similar itch as my fine art practice but did not have all the conceptual and academic demands around its meaning. I followed this path and here we are 22 years later.
What originally drew you to metalwork? What sets metal apart from other materials you’ve worked with?
I think the immediacy of shape and the ability to change it just as quickly is what originally drew me in.
How does your early career and previous experience in the industry influence your work today?
I don’t see what we do at Chris French Metal as art. I guess I would say that studying art gave me a language to talk about what I see. I’ve always been a looker, someone who notices the nuances in the ordinary, but it wasn’t until studying art at ASU that I had access to the words to describe this skill set.
Tell me about your process. How closely do you work with clients? Describe your relationship with the architect and contractor.
We like to get involved early and ask a lot of questions. Most of the work we do is heavily integrated into the architecture and requires that we are involved with the entire process. I prefer some direction.
Who is on your team? Is collaboration important to your process?
Eleven of the best people you could ask for – my wife and I run the company.
We have three Project Manager / Designers who take our proposals and design documents and dig in. They work hand in hand with Contractors, Structural Engineers, Waterproofing Engineers, Lighting Consultants, Architects, Interior Designers, Site Superintendents, Outside Vendors, Shop and Field Staff as well as with me personally. They run all the project specific purchasing and coordination.
We have a Facilities Coordinator who handles all our shipping and receiving, co-manages all purchase orders in our database, and helps get work through the shop and into the field.
We also have six shop staff who do all the fabrication and installation.
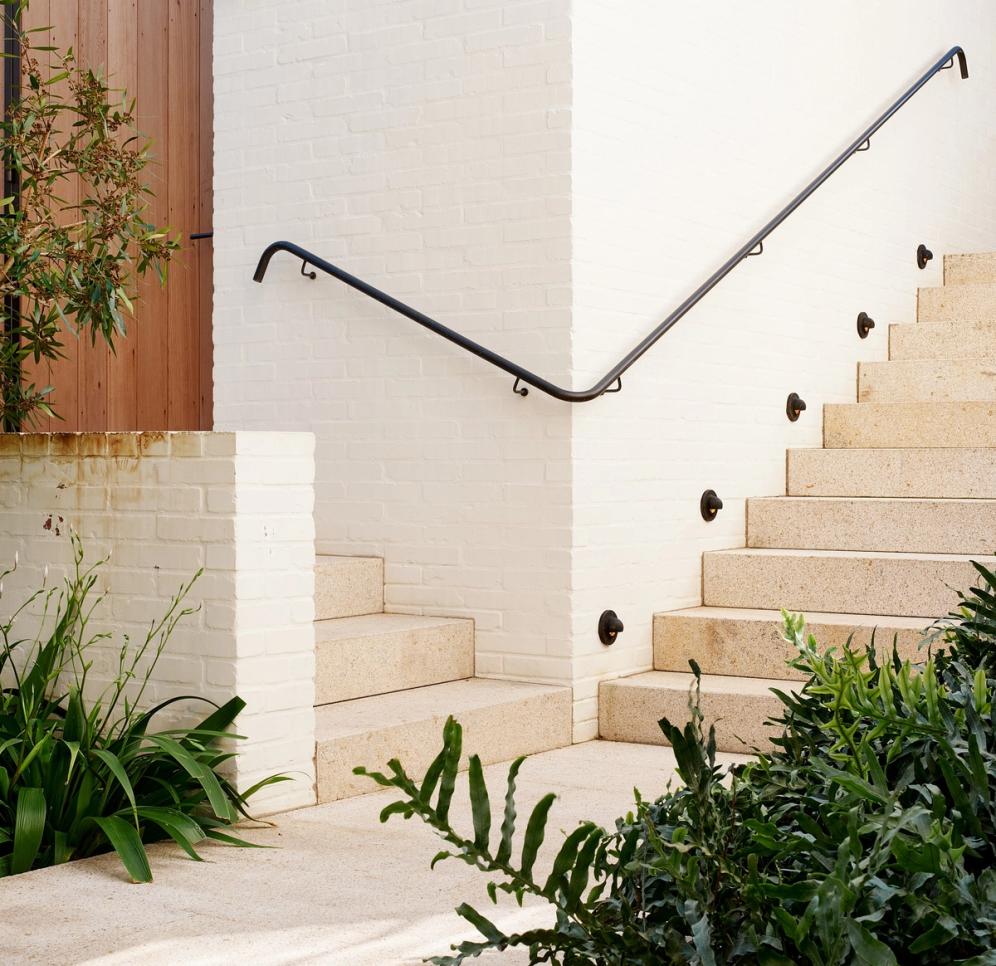
Tell me what it’s like to run a small business. What challenges have you faced and what has been rewarding about that?
For me, it’s an emotional roller coaster. There are such intense highs and lows, and they can all happen within hours of each other. I wear a lot of hats and they’re constantly swapped out throughout any given day. That said, it’s also very rewarding. I am supported by incredibly talented people who all love their work and show up every day to do their best, so I couldn’t ask for much more.
There have been too many challenges to list, but over the last 22 years the two biggest were the 2008 crash and COVID. We managed to make it through both of those, maintaining all of our staff, so we’re doing pretty good if you ask me!
Which new technologies have influenced your work as of late? How do you think they will change the industry going forward?
For us, it’s CNC machinery. We purchased our first CNC mill at the end of 2019, and it’s incredible what we’ve done with it and how much there still is to learn. Not everyone in the shop is well versed yet, but we’ll get there!
Our studio deeply values working with makers and artisans who are experts in their craft. What is special to you about high-quality, custom goods?
Those with the means and patience can get just about anything they want. We are fortunate to work with creative people who really know what they want, and we get to figure out how to provide it. The process is stimulating and keeps everyone engaged along the way, and can sometimes be frustrating and exhausting, but never boring and never easy!
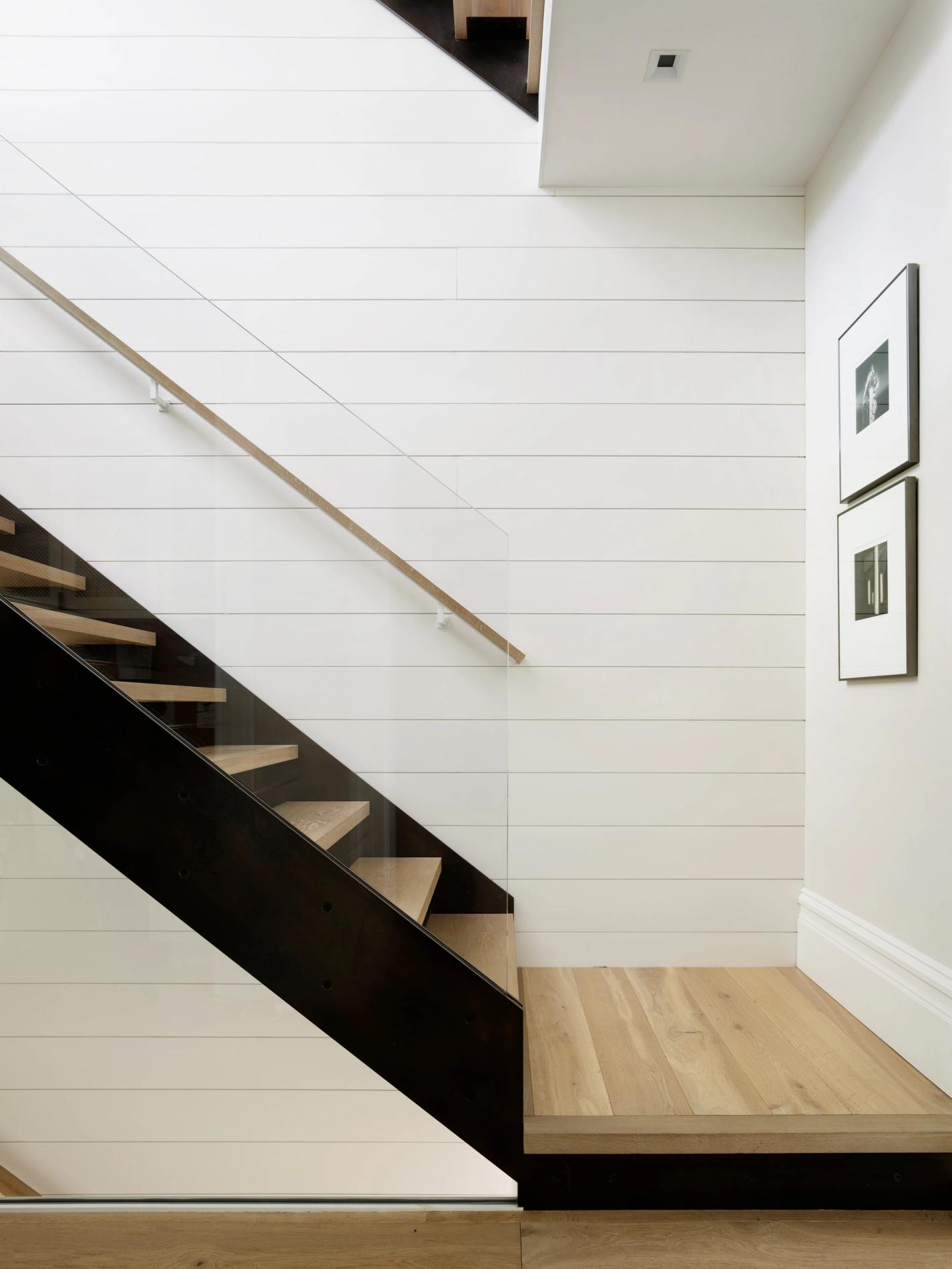